An HMC833 Frequency Synthesizer
Features
Fractional-N and integer modes.
24-bit step size: 3 Hz resolution typically.
Exact frequency mode.
Wide bandwidth: 25 to 6000 MHz.
Good phase noise performance: -120 dBc/Hz at 10 kHz offset (1 GHz carrier, on-board reference, 150 kHz LBW).
Dual outputs with flexible output amplifier configuration.
Design files are available at https://gitlab.com/dyadic-groups/rfblocks-hardware-modules/wideband_plo_2 (licensed under CERN-OHL-S v2).
Typical Performance Characteristics
Phase noise
Phase noise measurements shown in this section where made using an HP 11729C carrier noise test set with a Rohde & Schwarz SMHU signal generator as the reference. A full description of the measurement procedure is given here: Phase Noise Measurement with the HP11729C.
Figure 1: Measured phase noise at 1, 1.5, 2, 2.5 and 3 GHz with a loop bandwidth of 150 kHz.
Figure 2: Measured phase noise at 1 GHz for loop bandwidths of 5, 35, 75, and 150 kHz. See Table 2 for loop filter component values for each of the plotted bandwidths.
Figure 3: Measured phase noise as a function of carrier frequency at offset of 100Hz, 1kHz, 10kHz, 100kHz, 1MHz and 10MHz. PLO loop bandwidth is 150kHz.
Output power
The HMC833 VCO has a fundamental frequency range of 1500 to 3000 MHz. For frequencies below 1500 MHz a divider is used and for frequencies between 3000 and 6000 MHz a frequency doubler stage is used.
For frequencies below 1500 MHz a divider stage amplifier with a gain of approximately 3 dB may be used to compensate for losses in the divider. An output buffer amplifier may also be used across all frequencies and has four gain settings of 0, 3, 6 and 9 dB.
Figures 4a and 4b show the effect of the output buffer amplifier gain
settings on module output power. For the measurements shown in Figure 4a
the module is configured with the resistive splitter (R28
, R29
, R30
) but
no output amplifiers. For the measurements shown in Figure 4b the module
is configured with the resistive splitter and SKY65017 output amplifiers. In
both cases the divider stage amplifier is enabled to compensate for
divider losses at frequencies less that 1500 MHz. (See Hardware Configurations for a
description of the different module harware configurations.)
Figure 4a: Module output power. The integrated output power measured at the four available output buffer gain levels.
Figure 4b: Module output power with SKY65017 Amplifier. The integrated output power measured at the four available output buffer gain levels. An SKY65017 amplifier is used on each of the board outputs.
Figure 5a: Module output power with HMC833 buffer gain adjusted to reduce output power variation (no RF output amplifier).
Figure 5b: Module output power with HMC833 buffer gain adjusted to reduce output power variation (SKY65017 RF output amplifier).
Module Board Connector Configuration
Board Pin |
Type |
Description |
---|---|---|
|
Output |
Lock Detect, or Serial Data, |
or General Purpose (CMOS) Logic Output (GPO) |
||
|
Input |
Serial control data clock |
|
Input |
Serial control data |
|
Input |
Serial port enable signal |
|
Input |
Synthesizer reference select signal |
|
Power Input |
Main 10V DC power input |
|
Power Input |
Output amplifier DC power input |
|
Power Input |
Module ground |
|
Signal Input |
Female MMCX connector for external synthesizer |
reference signal input. |
||
|
Signal Input |
Female MMCX connector for optional input of |
synthesizer VCO tuning voltage. |
||
|
Signal Output |
Synthesizer RF output, channel A |
|
Signal Output |
Synthesizer RF output, channel B |
Figure 6: Synthesizer module connector layout.
Hardware Configurations
A number of board modifications are possible in order to change the hardware configuration. These are:
A choice of two module board variants. One makes use of SOT-89 case style output amplifiers, the other makes use of the DFN-6 case style.
A resistive splitter on the HMC833 RF output. This allows either a single or dual RF power output for the board.
Provision for Minicircuits LTCC ceramic filters in the RF output paths. If no filtering is required a 1206 style 0 ohm link or Minicircuits TPCN series LTCC thru-line can be used.
For the SOT-89 module board variant the output amplifer(s) may be replaced with 1206 style 0 ohm links for unamplified RF power output.
Optionally, the HMC833 Vtune signal may be taken from an external source by populating
R24
with a 0 ohm link and ensuring thatR9
,C19
andC20
are left unpopulated.
SOT-89 output amplifier board variant
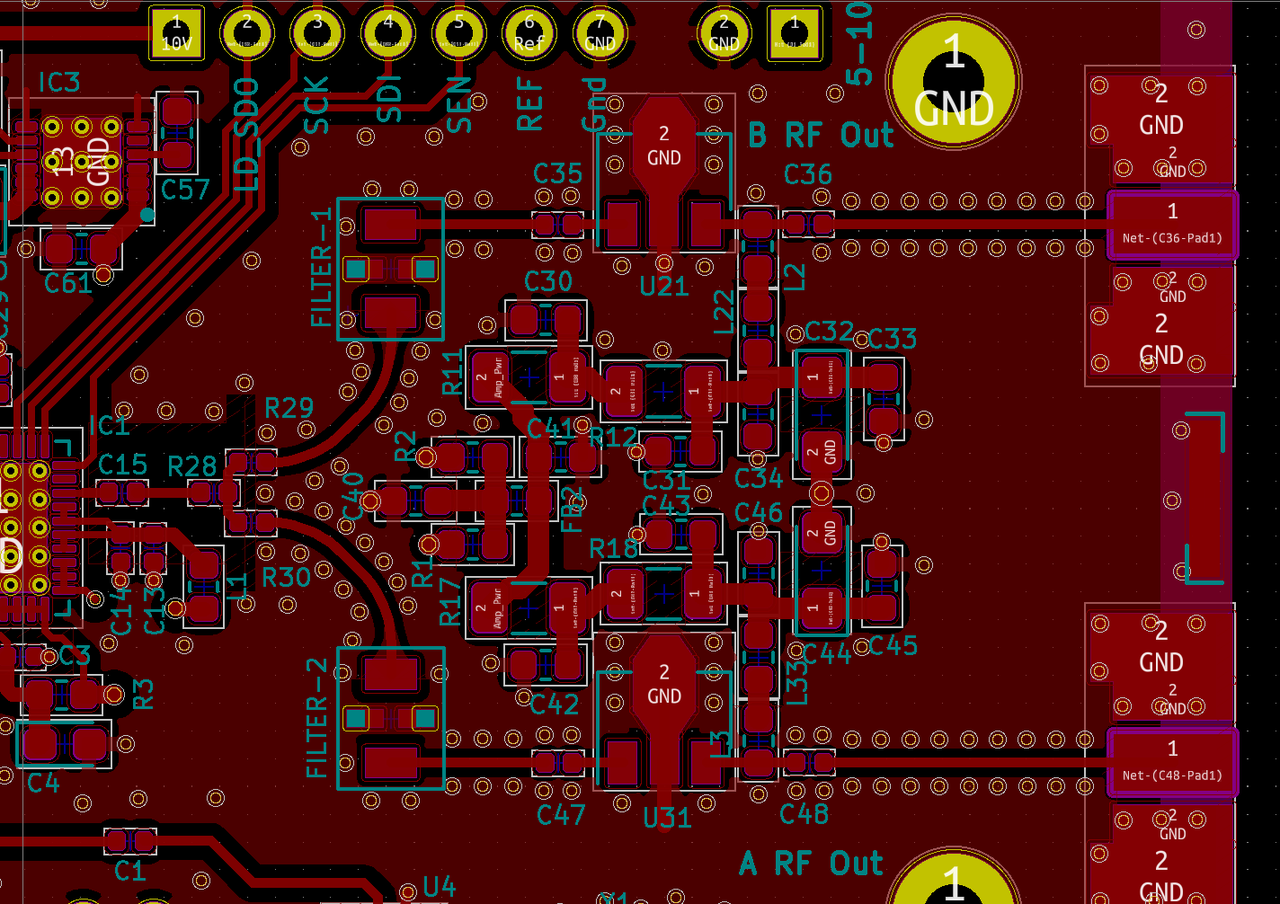
Figure 7a: SOT-89 board variant RF output path layout.
Figure 7b: SOT-89 output amplifier design.
For broadband use the SKY65017 performs reasonably well with relatively flat gain of about 18 dB out to 5GHz and a OIP1 of 20 dBm (typical). See SKY65017 broadband gain block for S-parameter measurements of the standalone gain block.
For a more modest gain of about 15 dB and OIP1 of 18 dBm (typical) the SKY65014 offers better return loss characteristics. See SKY65014 general purpose gain block for S-parameter measurements of the standalone gain block.
DFN-6 output amplifier board variant
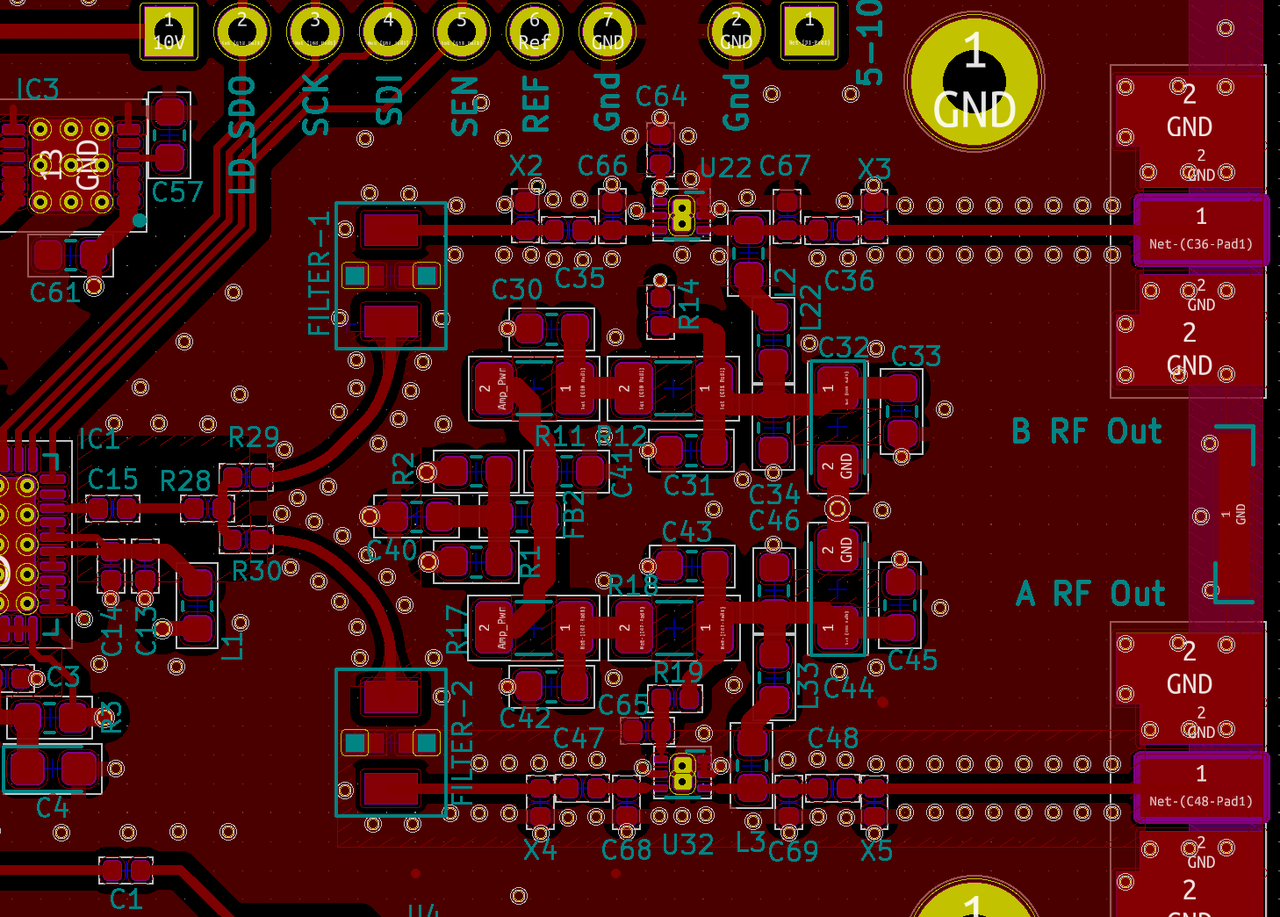
Figure 8a: DFN-6 board variant RF output path layout.
Figure 8b: DFN-6 output amplifier design.
Applications Information
Figure 9 illustrates the minimal setup for controlling the synthesizer board. The board is connected to Pico board controller which is running the ECApp embedded control firmware. Synthesizer board pins are described in Table 1 with Figure 6 showing the layout of the board pins and RF connectors on the rear of the board.
Figure 9: Minimal synthesizer board control
The rfblocks Python package provides the HMC833Controller class which is used to control the board. The following code snippet shows a small example:
>>> from rfblocks import hmc833, HMC833Controller, create_serial >>> ser_device = '/dev/tty.usbmodem14201' >>> ser = create_serial(ser_device) >>> plo = hmc833(sen='G17', ld_sdo='G16') >>> ctl = HMC833Controller('plo1', plo) >>> lock = ctl.initialize(ser) >>> lock True >>> ctl.freq = 1500 >>> lock = ctl.configure_freq(ser) >>> ctl.buffer_gain = hmc833.OutputBufferGain.MAXGAIN >>> ctl.configure_gains(ser) >>> lock = ctl.check_plo_lock(ser) >>> lock True >>> ctl.vco_mute = True >>> ctl.configure_vco_mute(ser) >>> ctl.vco_mute = False >>> ctl.configure_vco_mute(ser)
The code does the following:
Import the
rfblocks
HMC833Controller
andhmc833
classes.Open the USB/RS-232 serial device which connects the host computer to the
ECApp
control firmware running on the controller board.Create an instance of the
hmc833
device class. The synthesizer board's serial enable line (sen
) is connected to the Pico controller board'sG17
GPIO (pin 22). The board's lock status pin is connected to theG16
GPIO (pin 21). The board'sREF
pin is left unconnected. Since theREF
pin is pulled high on the board the internal 50MHz reference is used.Create an instance of
HMC833Controller
and initialize the synthesizer. Initialization will set the synthesizer output signal frequency toHMC833Controller.DEFAULT_PLO_FREQ
and the output gain tohmc833.OutputBufferGain.MAXGAIN_MINUS_9DB
. The status of the PLL lock is returned.The synthesizer output signal frequency is set to 1500 MHz.
The synthesizer output gain is set to maximum. For output frequencies less than 1500 MHz the synthesizer output divider is used and extra gain of approximately 3dB is available by setting
HMC833Controller.divider_gain
tohmc833.DividerGain.MAXGAIN
. However, this increases the non-linearity of the output signal chain.Lastly, the RF output level is muted and then re-enabled.
Reference source
The synthesizer is switchable between the on board TXO based reference and
an external reference. Switching is done via U4
which is controlled by
the Ref
module pin.
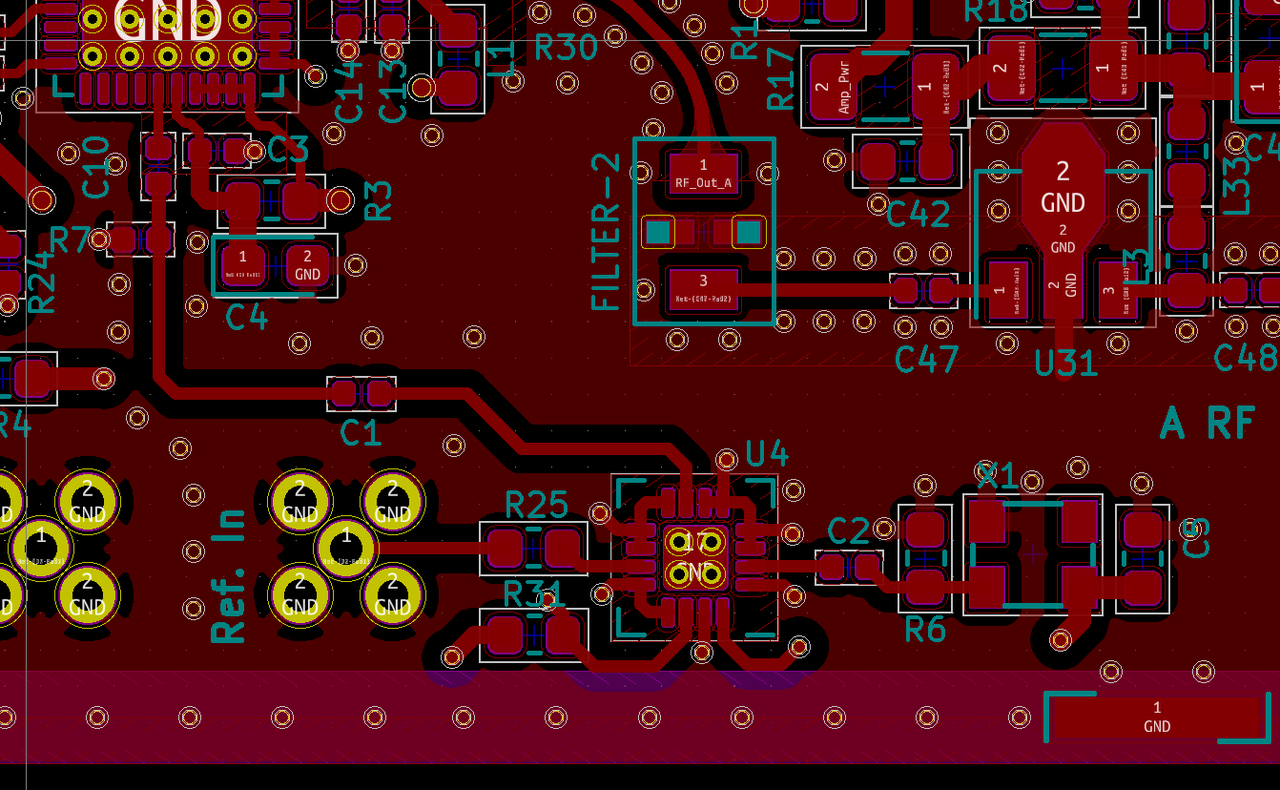
Figure 10a: Synthesizer reference switching layout.
Figure 10b: Synthesizer reference switching design
The Ref
module pin will be connected to a controller pin and this
controller pin used when configuring the PLO device using the
rfblocks.hmc833 class. The code snippet below illustrates the use of the
switchable reference source and configuring different reference
frequencies.
>>> from rfblocks import hmc833, HMC833Controller, create_serial, write_cmd >>> ser_dev = '/dev/cu.usbmodem14201' >>> ser = create_serial(ser_dev) >>> plo = hmc833(sen='D0', ld_sdo='C4', ref='D1', fref=100.0, refdiv=1, refsrc=hmc833.ReferenceSource.EXTERNAL) >>> ctl = HMC833Controller('plo1', plo) >>> ctl.initialize(ser) True >>> ctl.freq = 500 >>> ctl.configure_freq(ser) True >>> ctl.refsrc = hmc833.ReferenceSource.INTERNAL >>> ctl.ref_freq = 50.0 >>> ctl.ref_div = 1 >>> ctl.configure_refsrc(ser) >>> ctl.refsrc = hmc833.ReferenceSource.EXTERNAL >>> ctl.ref_freq = 160.0 >>> ctl.ref_div = 2 >>> ctl.configure_refsrc(ser) >>> ctl.ref_freq = 70.0 >>> ctl.ref_div = 1 >>> ctl.configure_refsrc(ser)
The Low Spurious RF Signal Generator reference design uses an rfblocks application which makes use of a second HMC833 synthesizer as an external reference source. The frequency of this reference source is varied with changes in the output frequency of the signal generator so as to minimize spurs.
Phase detector frequency
In most applications the PLO phase detector frequency, \(f_{PD}\), remains constant. However, in some applications \(f_{PD}\) may vary as the PLO is tuned over it's band of operation. For example this would be the case where the PLO input reference frequency is varied in order to minimize the generation of spurious signals.
Variations in \(f_{PD}\) may cause non-linearities in the charge pump and phase detector. When operating the PLO in fractional mode these non-linearities will degrade performance. The following description is taken from the HMC832 data sheet.
In fractional mode, charge pump linearity is of paramount importance. Any nonlinearity degrades phase noise and spurious performance. These nonlinearities are eliminated by operating the phase detector with an average phase offset, either positive or negative (either the reference or the VCO edge always leads, that is, arrives first at the phase detector).
A programmable charge pump offset current source adds dc current to the loop filter and creates the desired phase offset. Positive current causes the VCO to lead, whereas negative current causes the reference to lead.
The charge pump offset is controlled via HMC833 register 0x09. Increasing the offset current causes the phase offset to scale from 0 to 360 degrees. The specific level of charge pump offset current (HMC833 register 0x09, bits[20:14]) is calculated using the equation below and shown in Figure 10.
- where: \(f_{PD}\) is the comparison frequency of the phase detector (in
-
Hz), \(I_{CP}\) is the full scale setting (in A) of the charge pump (set in HMC833 register 0x09[6:0] and register 0x09[13:7]).
Note that the required charge pump offset current must not exceed 25% of the programmed charge pump current. It is recommended to enable the down offset and disable the up offset by writing HMC833 register 0x09[22:21] = 10b.
Figure 10: Recommended Charge Pump Offset Current vs. Phase Detector Frequency for Typical Charge Pump Gain Currents (taken from the HMC832 data sheet)
Reference Designs
Design Notes
The board components are the synthesizer core, loop filter, PLL reference, synthesizer signal output, power supply regulation and control connections. The guiding design principle is to keep noise on the VCO tune line and power supplies to an absolute minimum. Placement of and routing between board components is critical in achieving this.
Figure 9: Block level board layout.
Power supply regulators are kept as far from RF signal paths as is practical. In addition, separate power supply regulators are used for the synthesizer VCO supply, the on-board reference oscillator supply, the charge pump supply and the general 3.3V power supply.
Signal output from the HMC833
synthesizer core is split using a 6dB
resistive splitter (R28, R29, R30
). The resulting dual signal path
then passes through amplifiers U2
and U3
. These are placed as far
as possible from the power supply regulators and loop filter signal
path.
Loop filter
The PLL charge pump output is from pin 4 of IC1
. This signal is
denoted as Vtune
in Figure 10. In normal operation, Vtune
passes
through the PLL loop filter which consists of C16
, R10
, C24
,
R8
, C17
, C18
, R9
, C19
and C20
and delivered to pin 23 of
IC1
. This configuration allows for the use of passive filters up
to 4 poles (5th order loop filter). Table 2 lists some example loop
filter configurations for the HMC833. The component values shown in
Figure 10 correspond to the 3rd entry in Table 2 with a loop bandwidth
of 155 kHz. The other entries in the table are taken from the HMC833
data sheet (p9, Loop Filter Configuration Table).
Figure 11: Loop Filter Component Layout
The primary factor determining the layout of the loop filter
components is to reduce the possibility of spurious signals coupling
to the Vtune
signal path. To assist with this the final section of
the Vtune
signal path (shown in dark green in Figure 10) is routed
via an internal copper layer on the board which is sandwiched between
two ground planes. This will reduce the possibility of output RF
signal energy being coupled to Vtune
. In addition to this, the
loop filter components are specified as 0805 size components to ease
the task of modifying the loop filter configuration.
To expand the utility of the board and to make the HMC833 available
for use as a 'discrete' VCO, the Vtune
signal can be driven from
external sources via the VTune In
board connector by populating
R24
and removing R9
.
Loop Filter BW |
C16 |
C24 |
C18 |
R10 (Ohm) |
R8 (Ohm) |
R9 (Ohm) |
---|---|---|---|---|---|---|
5 kHz |
33n |
1.0u |
3.3n |
59 |
3300 |
0 |
35 kHz |
2.2n |
22n |
1.0n |
470 |
1000 |
0 |
75 kHz |
560p |
5.6n |
100p |
1000 |
2000 |
0 |
100 kHz |
270p |
3.3n |
82p |
1500 |
2700 |
0 |
150 kHz |
100p |
3.3n |
10p |
1430 |
10000 |
0 |
Synthesizer reference
The on-board reference for the synthesizer is a reasonably good quality temperature compensated crystal oscillator. The measured phase noise for this reference is shown in Figure 12. The overall phase noise of the synthesizer is quite good with this reference at -120 dBc/Hz at 10 kHz offset for a carrier frequency of 1 GHz. The synthesizer phase noise is sensitive to the reference phase noise. Using a higher quality external reference could improve the synthesizer phase noise by 5 dB.
Figure 12: On-board Reference Phase Noise.
For the purposes of modelling the characteristics of the PLO design using Analog Devices ADIsimPLL PLL synthesizer design software, the phase noise model shown below in Table 3 is used.
Freq. (Hz) |
PN (dBc/Hz) |
---|---|
100 |
-100 |
500 |
-118 |
1.00k |
-126 |
5.00k |
-140 |
10.0k |
-143 |
50.0k |
-148 |
100k |
-150 |
500k |
-150 |
1.00M |
-155 |
5.00M |
-160 |
Signal output
Synthesizer signal output is generally via the resistive divider
R28
, R29
, and R30
. However, if only a single RF output is
desired then R28
and R30
should be replaced by \(0\Omega\) links
and R29
left unpopulated. The signal path is then through output
amplifiers U2
, U3
. Three variants of the synthesizer board allow
for the use of amplifiers in SOT-86, SOT-89, or DFN6 packages.
Power for amplifiers may be taken either from the primary 10V board
supply (via R2
) or from the separate amplifier power input via J1
and R1
. Together with R11
, R12
, R17
, and R18
this allows
for some flexibility in limiting power dissipation on the board while
providing the correct amplifier voltage and current supply.
Power regulation
Good power regulation is crucial for getting the most out the HMC833.
In particular, very low noise regulators should be used for VCC1
, VCC2
,
VDDLS
, and VPPCP
. The current supply requirements for the HMC833
is given in Table 4.
Supply |
Voltage |
Current |
---|---|---|
|
5V |
8mA |
|
5V |
100mA |
|
5V |
105mA |
|
3.3V |
52mA |
Texas Instruments TPS717-Q1
series and LP38798
are used for regulating the
above supplies because of their very low noise and excellent PSRR.
The LP38798
has typically 5.4 \(\mu V_{(\textrm{RMS})}\) integrated noise
from 10 Hz to 100 kHz (input voltage 6V, output voltage 5V) and better than
60 dB of PSRR across the same frequency range with better than 40 dB PSRR
up to 2 MHz. The TPS717-Q1
has similar performance.
These characteristics are of special importance for the VCO supplies
since any noise on these will result in spurious signals in the
synthesizer output.
The maximum output current for the TPS717-Q1
regulators is 150mA and
for the LP38798
, 800mA. A TPS71750
is therefore used for
the VPPCP
, VDDLS
supply and a TPS71733
is used for the
AVDD
, VCCPD
, VCCPS
, VCCHF
, RVDD
supply.
An LP38798
is used for both the VCC1
and VCC2
supplies.
In addition, a TPS71733
is used to regulate the supply for the
(optional) on-board reference oscillator.
The absolute maximum input voltage for the TPS717
regulators is 7V.
An on board MIC5209YM regulator is therefore implemented to provide a
regulated 6V, 500mA supply. The 6V supply also serves as the input for
the LP38798
in order to minimize the overall power dissipation.
Note that the ESR of the output capacitor on the TPS717
devices must be
less that \(1\Omega\). This constraint is met by using a 0603 MLCC such
as CC0603KRX5R8BB105 or GCM188R71C105KA64D on the output.
(Note also that X5R or X7R dielectrics should be used.)
The LP38798 is stable with an output capacitance of 1 uF to 10 uF. Since this will supply the VCO and output buffer the use of an MLCC is avoided in favour of a low ESR tantalum capacitor. This choice eliminates the possibility of microphonics on the supply rail.
Control connections
Serial programming connections:
SEN should be connected to a general purpose output pin. Note that this pin must be LOW on power up. When connected to a controller, the controller pin will be tristated initially (after power on or reset) and then configured as an output pin in the LOW state.
SCK is connected to the SPI SCK pin.
SDI is connected to the SPI MOSI pin.
It's not clear as yet which controller pin the LD_SDO should be connected to.
When using the SPI driver board for testing, the 'A' line on the SPI driver should be connected to the HMC833 SEN pin.
Scripts
Measuring output power
Figures 13a and 13b illustrates the test setup used to measure the HMC833 PLO power output. Since we don't currently have access to a spectrum analyzer which covers the full frequency range of the HMC833 the measurements are carried out in two stages. An HP8560A spectrum analyzer is used to measure the peak power of the fundamental tone for the frequency range 0.1 to 2.8 GHz. The power meter reference design is then used to measure the integrated power output from 0.1 to 6 GHz. Up to the power measurement uncertainties there is negligible difference between the integrated and peak power above approximately 1 GHz. Comparison of the measurements taken using both methods in the frequency range 0.1 to 2.8 GHz confirms this.
When using the power meter a 24 dB attenuator is connected between the
power measurement sensor head and the signal source. This configuration
must be calibrated before use. Previously measured calibration files are
available here: referencedesigns/PowerMeter/app/cal-files
. The default
calibration file is 24dB-atten-48-0007-Det3-100-6000MHz.json
which is
used with the combination of the 24 dB attenuator with serial number
0007
together with the measurement sensor head labelled Det3
. Refer
to the Calibration and correction section of the power meter documentation
for a description of how to generate calibration files.
The test setup makes use of the same layout as shown in Figure 9. The pin assignments and serial device may need to be changed in the script. The following code fragments can be used to make these changes before exporting the script.
Figure 13a: HMC833 PLO power output test setup, 0.1 to 2.85 GHz.
Figure 13b: HMC833 PLO power output test setup, 0.1 to 6 GHz.
# # Generated from hmc833.org # import sys from time import sleep from pathlib import Path import json import numpy as np from scipy import ( interpolate ) import rpyc from rfblocks import hmc833, HMC833Controller, create_serial from tam import ( InstrumentMgr, InstrumentInitializeException, UnknownInstrumentModelException, HP8560A_GPIBID, SMHU58_GPIBID ) <<serial-port>> <<pin-assignment>> do_stage_1 = False do_stage_2 = False do_stage_3 = True ref_level = 20.0 sa_cal_file = 'hmc833-pwr-sa-cal.json' pwrmeter_cal_file = 'PowerMeter/app/cal-files/24dB-atten-48-0007-Det3-100-6000MHz.json' stage1_measurements_file = 'hmc833-output-pwr-stage-1.json' stage2_measurements_file = 'hmc833-output-pwr-stage-2.json' stage3_measurements_file = 'hmc833-output-pwr-stage-3.json' loss_fn = None def insertion_loss(freq): return float(loss_fn(freq)) def measure_sigpwr(): sig_pwr = {} for f in freq_list: print(f'{f=}:', end='') plo_ctl.freq = f is_locked = plo_ctl.configure_freq(ser) if is_locked: pwr, _ = sa.measure_pwr(f) sleep(0.5) sig_pwr['{:.1f}'.format(f)] = pwr + insertion_loss(f) print(f', {pwr+insertion_loss(f)}') else: print(', PLO lock failed!') return sig_pwr def measure_integrated_pwr(): sig_pwr = {} for f in freq_list: print(f'{f=}:', end='') plo_ctl.freq = f is_locked = plo_ctl.configure_freq(ser) if is_locked: chan_ctl.freq = f pwrmeter.root.measure(pwr_meter_chan) sig_pwr['{:.1f}'.format(f)] = float(chan_ctl.pwr) print(f', {chan_ctl.pwr}') else: print(', PLO lock failed!') return sig_pwr def measure_equalized_power(): sig_pwr = {} for f in freq_list: print(f'{f=}:', end='') if f < 1500.0: plo_ctl.divider_gain = hmc833.DividerGain.MAXGAIN elif f >= 3000.0: plo_ctl.buffer_gain = hmc833.OutputBufferGain.MAXGAIN_MINUS_3DB elif f >= 4400.0: plo_ctl.buffer_gain = hmc833.OutputBufferGain.MAXGAIN plo_ctl.freq = f is_locked = plo_ctl.configure(ser) if is_locked: chan_ctl.freq = f pwrmeter.root.measure(pwr_meter_chan) sig_pwr['{:.1f}'.format(f)] = float(chan_ctl.pwr) print(f', {chan_ctl.pwr}') else: print(', PLO lock failed!') return sig_pwr def calibrate(srcpwr, start_freq, stop_freq, step_freq): loss = {} sg.output = True for f in np.arange(start_freq, stop_freq, step_freq): # Note that the property assignment here may actually # be a rpyc remote operation depending on the selected # calibration device. Since ~f~ (and possibly ~srcpwr~) # may be numpy array scalars it is necessary to explicitly # cast these to standard Python float values. If this is # not done the remote rpyc process will almost certainly # generate strange numpy related exceptions. sig_freq = float(f) sg.freq = sig_freq sg.level = float(srcpwr) sleep(0.5) meas_pwr, _ = sa.measure_pwr(sig_freq) loss[sig_freq] = srcpwr - meas_pwr sleep(0.5) sg.output = False freqs = np.array([f for f in loss.keys()]) loss_arr = np.array([v for v in loss.values()]) loss_interp_fn = interpolate.interp1d( freqs, loss_arr, kind='cubic') with open(sa_cal_file, 'w') as fd: json.dump(loss, fd) return loss_interp_fn # Test HMC833 PLO initialization ser = create_serial(serial_device) plo = hmc833(sen=PLO_SEN, ld_sdo=PLO_LD_SDO) plo_ctl = HMC833Controller('plo1', plo) plo_ctl.initialize(ser) if do_stage_1 is True: print() print("""---------- Stage 1 ----------\n""") print("""Output power measurements from 0.1 to 2.85 GHz.""") print("""These measurements use the HP8560A spectrum analyzer.""") input("Press a key when ready... ") print() # Spectrum analyzer initialization instrument_mgr = InstrumentMgr() try: sa = instrument_mgr.open_instrument('HP8560A', HP8560A_GPIBID) except InstrumentInitializeException as iie: print(iie.message) sys.exit(-2) except UnknownInstrumentModelException as ume: print(ume.message) sys.exit(-3) sa.clear() sa.vavg = 2 sa.fspan = 0.1 sa.ref_level = ref_level use_existing_sa_cal = False cal_path = Path('./'+sa_cal_file) if cal_path.is_file(): print("""There is an existing test cable calibration file: {}. Would you like to use this?""".format(sa_cal_file)) ch = input("Use existing cable cal. file? (Y/N): ") if ch[0] in ['y', 'Y']: use_existing_sa_cal = True if not use_existing_sa_cal: try: sg = instrument_mgr.open_instrument('SMHU58', SMHU58_GPIBID) except InstrumentInitializeException as iie: print(iie.message) sys.exit(-2) except UnknownInstrumentModelException as ume: print(ume.message) sys.exit(-3) print("""Calibration of the test cable must now be carried out. Please connect the test cable between the RF output of the SMHU58 signal generator and the HP8560A spectrum analyzer.""") input("Press a key when ready... ") loss_fn = calibrate(0.0, 100.0, 2850.0, 100.0) print("Calibration complete.") else: with open(sa_cal_file) as fd: loss = json.load(fd) freqs = np.array([float(f) for f in loss.keys()]) loss_arr = np.array([v for v in loss.values()]) loss_fn = interpolate.interp1d( freqs, loss_arr, kind='cubic') print("Cable calibration data loaded from '{}'".format(sa_cal_file)) print("""Please connect the test cable between the output of the RF signal generator under test and the input of the HP8560A spectrum analyzer.""") input("Press a key when ready... ") freq_list = [float(f) for f in np.linspace(100.0, 2800.0, 40).round()] plo_ctl.divider_gain = hmc833.DividerGain.MAXGAIN plo_ctl.vco_mute = False print("Gain setting: MAXGAIN_MINUS_9DB...") plo_ctl.buffer_gain = hmc833.OutputBufferGain.MAXGAIN_MINUS_9DB plo_ctl.configure(ser) sa.clear() sleep(2.0) sa.vavg = 2 sa.fspan = 0.1 sa.ref_level = ref_level max_minus_9dB = measure_sigpwr() print("Gain setting: MAXGAIN_MINUS_6DB...") plo_ctl.buffer_gain = hmc833.OutputBufferGain.MAXGAIN_MINUS_6DB plo_ctl.configure(ser) sa.clear() sa.vavg = 2 sa.fspan = 0.1 sa.ref_level = ref_level max_minus_6dB = measure_sigpwr() print("Gain setting: MAXGAIN_MINUS_3DB...") plo_ctl.buffer_gain = hmc833.OutputBufferGain.MAXGAIN_MINUS_3DB plo_ctl.configure(ser) sa.clear() sa.vavg = 2 sa.fspan = 0.1 sa.ref_level = ref_level max_minus_3dB = measure_sigpwr() print("Gain setting: MAXGAIN...") plo_ctl.buffer_gain = hmc833.OutputBufferGain.MAXGAIN plo_ctl.configure(ser) sa.clear() sa.vavg = 2 sa.fspan = 0.1 sa.ref_level = ref_level maxgain = measure_sigpwr() stage_1 = {'max_minus_9dB': max_minus_9dB, 'max_minus_6dB': max_minus_6dB, 'max_minus_3dB': max_minus_3dB, 'maxgain': maxgain} # Stash the measurements obtained so far with open(stage1_measurements_file, 'w') as fd: json.dump(stage_1, fd) plo_ctl.vco_mute = True plo_ctl.configure(ser) if do_stage_2 is True: print() print("""---------- Stage 2 ----------\n""") print("""Output power measurements from 0.1 to 6 GHz.""") print("""Please attach the power meter 0.1-6GHz measurement head to the HMC833 PLO module RF output. Ensure that the measurement head is connected as channel 0 on the power meter base unit and that the pwrmeter app is running.""") input("Press a key when ready... ") print() # Power meter initialization. pwrmeter = rpyc.connect('127.0.0.1', 18863) pwrmeter.root.initialize() chan_controllers = pwrmeter.root.detectors pwr_meter_chan = 0 chan_ctl = chan_controllers[pwr_meter_chan] chan_controllers[1].enabled = False chan_ctl.load_caldata(pwrmeter_cal_file) chan_ctl.apply_correction = True freq_list = [float(f) for f in np.linspace(100.0, 6000.0, 50).round()] plo_ctl.divider_gain = int(hmc833.DividerGain.MAXGAIN) plo_ctl.vco_mute = False print("Gain setting: MAXGAIN_MINUS_9DB...") plo_ctl.buffer_gain = hmc833.OutputBufferGain.MAXGAIN_MINUS_9DB plo_ctl.configure(ser) max_minus_9dB = measure_integrated_pwr() print("Gain setting: MAXGAIN_MINUS_6DB...") plo_ctl.buffer_gain = hmc833.OutputBufferGain.MAXGAIN_MINUS_6DB plo_ctl.configure(ser) max_minus_6dB = measure_integrated_pwr() print("Gain setting: MAXGAIN_MINUS_3DB...") plo_ctl.buffer_gain = hmc833.OutputBufferGain.MAXGAIN_MINUS_3DB plo_ctl.configure(ser) max_minus_3dB = measure_integrated_pwr() print("Gain setting: MAXGAIN...") plo_ctl.buffer_gain = hmc833.OutputBufferGain.MAXGAIN plo_ctl.configure(ser) maxgain = measure_integrated_pwr() stage_2 = {'max_minus_9dB': max_minus_9dB, 'max_minus_6dB': max_minus_6dB, 'max_minus_3dB': max_minus_3dB, 'maxgain': maxgain} # Stash the measurements obtained so far with open(stage2_measurements_file, 'w') as fd: json.dump(stage_2, fd) plo_ctl.vco_mute = True plo_ctl.configure(ser) if do_stage_3 is True: print() print("""---------- Stage 3 ----------\n""") print("""Output power measurements from 0.1 to 6 GHz.""") print("""Please attach the power meter 0.1-6GHz measurement head to the HMC833 PLO module RF output. Ensure that the measurement head is connected as channel 0 on the power meter base unit and that the pwrmeter app is running.""") input("Press a key when ready... ") print() # Power meter initialization. pwrmeter = rpyc.connect('127.0.0.1', 18863) pwrmeter.root.initialize() chan_controllers = pwrmeter.root.detectors pwr_meter_chan = 0 chan_ctl = chan_controllers[pwr_meter_chan] chan_controllers[1].enabled = False chan_ctl.load_caldata(pwrmeter_cal_file) chan_ctl.apply_correction = True freq_list = [float(f) for f in np.linspace(100.0, 6000.0, 50).round()] plo_ctl.divider_gain = int(hmc833.DividerGain.MAXGAIN) plo_ctl.vco_mute = False equalized_pwr = measure_equalized_power() stage_3 = {'equalized_pwr': equalized_pwr} # Stash the measurements obtained so far with open(stage3_measurements_file, 'w') as fd: json.dump(stage_3, fd) plo_ctl.vco_mute = True plo_ctl.configure(ser)